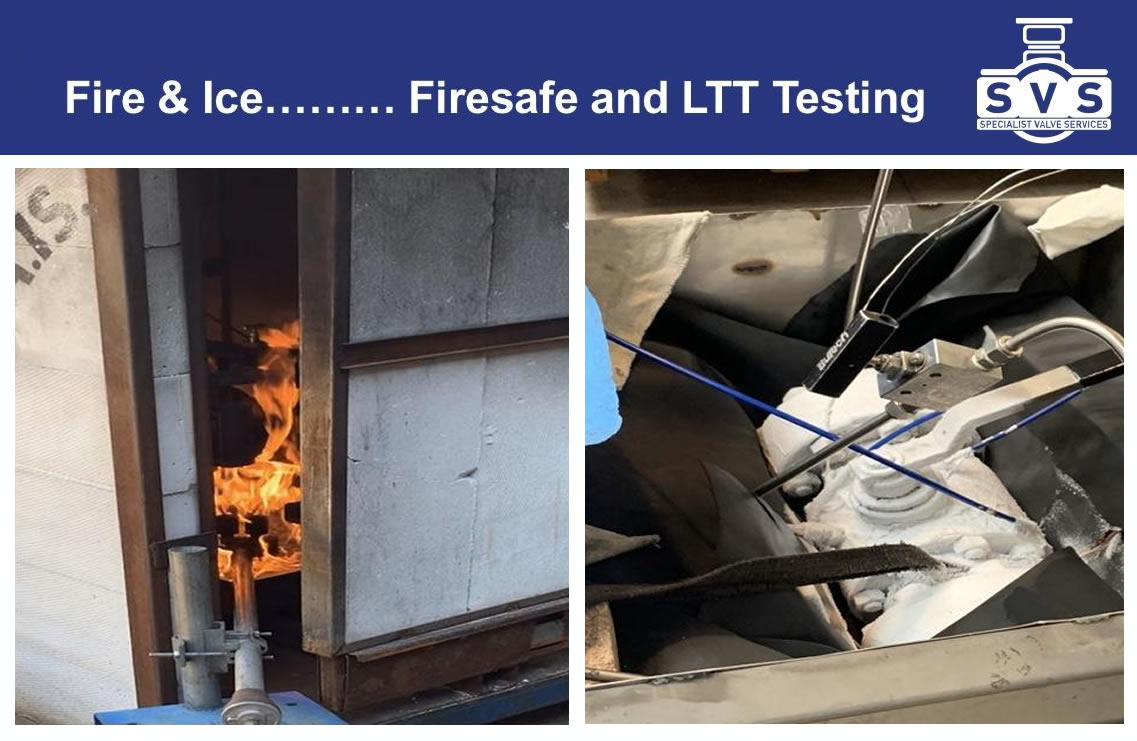
Firesafe and LTT Testing
SVS can carry out all aspects of specialised testing in close collaboration with our key manufacturers to meet client’s project needs, even on R & D requirements! We will work to the parameters required, enlisting the expertise of all the component manufacturers to ensure the best results.
Firesafe Testing
A critical and important industry required test to show that a valve can retain its integrity following a high temperature (750˚C - 1000 ˚C), monitored burning process to prove that following any given fire in service the valve can still provide the required shut off. As with any specialised testing, as design evolves, so does the testing parameters. We as a company are finding more and more end users looking for double isolation in line, and one of the best methods of achieving this is with a Double Block and Bleed ball valve (DBB).
The image shown is of just such a valve. Where there are gaps in the industry standards surrounding the burning of DBB designs, we have targeted this along with the manufacturers and the client directly to burn a valve to an individual test procedure to give the confidence that every potential instance of failure is checked.
This particular high specified, 4” class 2500 DBB valve manufactured by Indra SRL , the cavity pressure was measured at very short intervals to ensure no over pressurisation during the burn. SVS took this a step further to witness the test along with our client, and viewed a completely successful test.
By doing this we have given the client confidence in the valve design as well as proving the high quality of the product supplied.
Low Temperature Testing
When valves are subjected to low temperatures, a method to prove the integrity of the valve is a low temperature test to prove that a valve can operate successfully at such conditions without the risk of leakage. The test is determined along with the client as to the “operation” or “seal and survive” criteria.
Where a valve is to be operated at low temperatures then there is high focus on the elastomers utilised. As a generalisation a Lip seal type is best proven, however where these are not best suited to aggressive medium then there may be a requirement to utilise specialised o-rings.
This particular valve was for a large project with this aggressive service medium. The most suitable elastomer for the service was -6C short of the required temperature range. SVS carried out a risk analysis with the elastomer manufacturer on the use of this valve at such low temperature test, we worked also in conjunction with the valve manufacturer on the design and test parameters to assess every potential risk.
In a combined effort to prove this elastomer was fit for purpose, a bespoke test was carried out to prove that any glass transition of the o-ring would not affect the valve operation tight shut off. This test was witnessed at the manufacturer by SVS and shared with the end user. Thus proving the elastomer was suitable for the supply and again instilling the confidence in a high quality valve package.
Pushing the boundaries for our customers and manufacturers.”